Many engine failures come from insufficient lubrication. I have seen operators struggle with this problem. I believe grooves on main bearings address these issues by letting oil flow efficiently.
This groove helps continuous oil flow around the journal. It reduces friction and controls heat. The crankshaft gets oil more steadily. That leads to longer bearing life, improved engine performance, and fewer breakdowns.
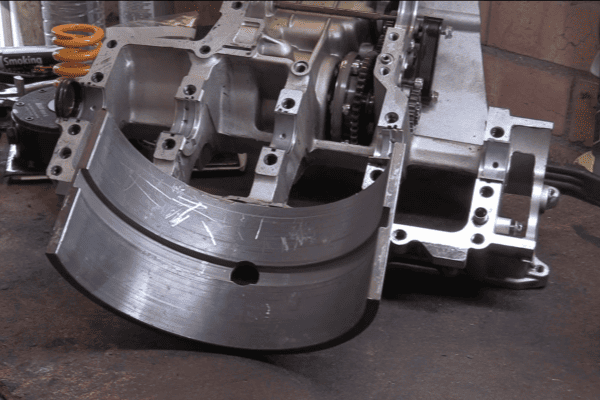
main bearing with oil groove
I want to explore two key questions about grooves on main bearings. I will look at where the groove is placed and how different groove styles compare. Let us begin.
Where is the groove on the main bearing?
I recall a friend’s truck that kept overheating. I discovered poor oil delivery from a misplaced bearing groove. I want to pinpoint the location and explain why it is crucial.
The groove lies on the bearing surface near the oil feed hole. It lines up with the main oil passage in the engine block. It guides the flow toward the crankshaft journal for smooth lubrication.
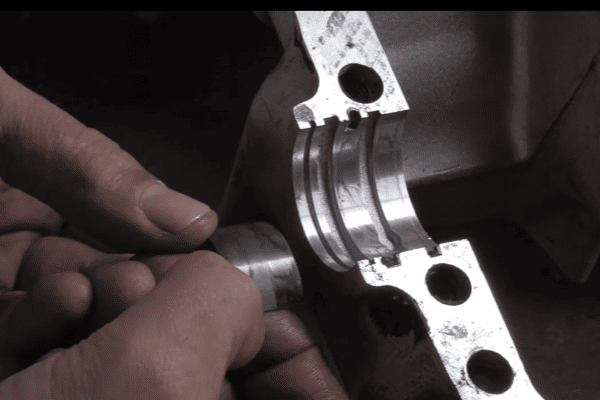
groove location on engine block
The significance of groove placement
The placement of the groove is not random. The bearing inserts rest in the main bearing housing. The groove usually aligns with the oil passage that comes from the engine block. The oil then goes into the groove and spreads across the bearing surface. If the groove is misaligned, the oil flow becomes inconsistent. This leads to excess friction and possible bearing damage.
I noticed this issue first-hand in my early days of working with engine components. I saw an engine teardown where the main bearing lacked proper alignment. The groove and the oil feed hole did not match. This small mistake caused a major repair. That experience taught me the importance of correct groove placement.
Why the location matters in lubrication
Lubrication efficiency depends on consistent oil flow. Oil is more than a lubricant. It also helps cool the bearing surfaces. When the groove is aligned correctly, it channels oil all around the bearing. It keeps the film of oil from breaking down. This prevents metal-to-metal contact, which can lead to hot spots or scoring.
Below is a simple table outlining how different groove placements affect performance:
Groove Placement | Effect on Lubrication | Common Result |
---|---|---|
Well-Aligned Groove | Steady oil distribution across bearing | Less friction, cooler operations |
Slightly Off Groove | Uneven oil film coverage | Possible localized heat and wear |
Badly Misaligned | Significant oil starvation | Rapid bearing failure, engine damage |
This table shows how important correct groove alignment is. The middle row might be the real challenge for many engines. Slight misalignment might not show a problem right away. But over time, that slight error can wear the bearing or cause unexpected temperature spikes.
I always double-check groove alignment when I source bearings. I run a quick test: hold the bearing shell in place and align it to the block’s oil feed. If it is off, I let my supplier know. The biggest lesson for me is not to compromise on details. Proper groove placement can be the difference between an engine that lasts and one that fails.
What is the difference between 1/2 groove and full groove main bearings?
I encountered confusion about half-groove bearings versus full-groove bearings. I understand that each style serves different applications. This question comes up often, so I want to clarify both types.
Half-groove bearings have a groove on only half of the bearing’s circumference. Full-groove bearings have grooves around their entire circumference. Each style has pros and cons.
Distinction based on groove coverage
Half-Groove Style
Half-groove bearings feature a groove that covers only one half of the bearing shell. This means the upper or lower half of the bearing gets a groove for lubrication, while the other half is smooth. That design aims for more contact area on the smooth side. This can increase load-carrying capacity. The idea is to keep a robust hydrodynamic film on the smooth portion, so higher load areas get better support. However, some worry that the oil supply might be less continuous.
Full-Groove Style
Full-groove bearings place a continuous groove around the entire 360 degrees. The oil flow is more widespread because it can circle the crankshaft journal. This design might reduce load capacity compared to half-groove bearings. The reason is that there is a smaller smooth section contacting the shaft. But many mechanics say full-groove bearings help keep the crankshaft fully oiled at all times. This can reduce the risk of dryness under heavy stress.
Here is a simple table:
Bearing Type | Groove Coverage | Pros | Cons |
---|---|---|---|
Half-Groove | 180° | More load surface, stable oil film | Possibly less constant oil feed, depends on RPM |
Full-Groove | 360° | Consistent oil supply, improved cooling | Lower load capacity, might wear faster |
Why choose one style over the other
My business supplies both styles because different engine designs demand unique lubrication approaches. Some older engines rely on half-groove bearings to handle higher loads. Modern engines often favor full-groove designs to ensure there is no oil starvation, especially under varied driving conditions.
I recall a large repair shop in Mexico that faced repeated bearing failures on older heavy trucks. They found out the original design needed half-groove bearings to handle the engine loads. They had switched to full-groove, hoping for better lubrication. They ended up with more wear on the bearings. That moment reminded me that engineering decisions often have trade-offs. Selecting the correct groove style is not always simple.
Another factor is engine speed and crankshaft design. Low-speed engines might do well with half-groove designs, while high-speed engines often want the full-groove design for even lubrication at high RPMs. The choice depends on the engine environment, the typical load, and the manufacturer’s recommendation.
I keep a close relationship with our OEM partners to confirm the best style for each engine application. My advice is: do not assume a full-groove design is always best. A quick check of the engine’s lubrication requirements will save a lot of hassle. It is also wise to remember the role of consistent oil pressure and quality. Even the best bearings fail without proper oil supply and correct alignment. This is another reason why I am so meticulous about confirming oil flow channels in any engine I work with.
Conclusion
Grooves on main bearings are key to proper lubrication. I choose the right style and align them carefully to keep engines running.